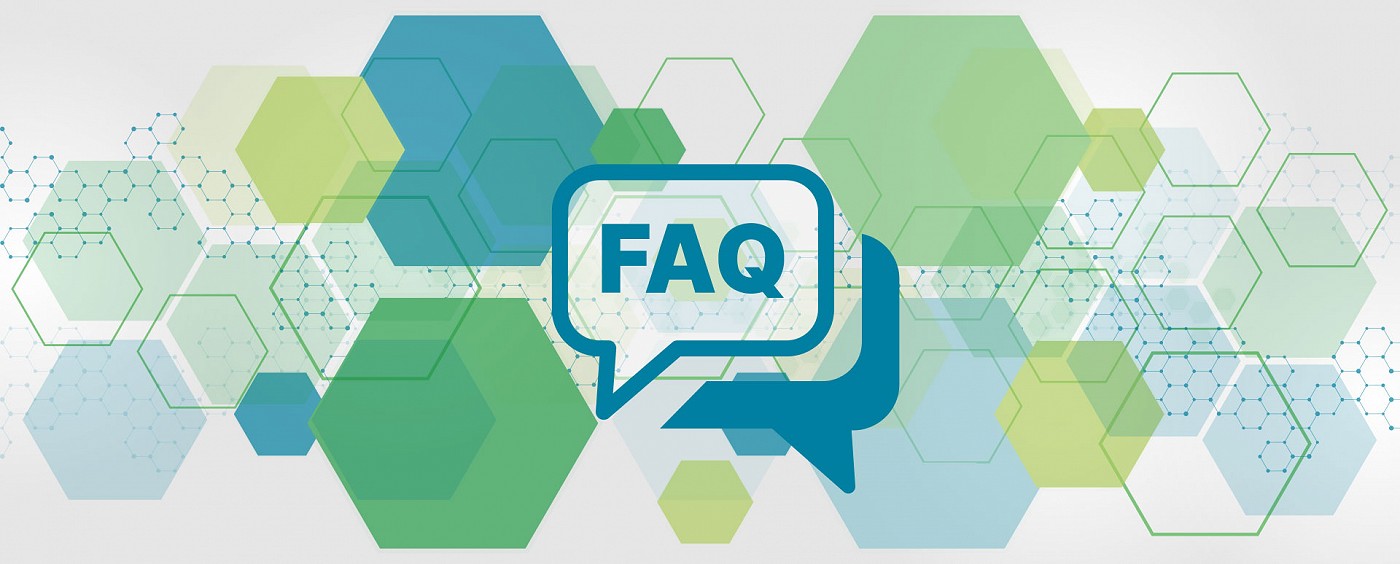
Frequently Asked Questions
The Clean Electronics Production Network unites diverse stakeholders working on an issue that spans global supply chains. If you are interested in more information or have a question that isn't answered here, please reach out to us at info@cleanelectronicsproduction.org
Some of your Questions:
- What is the Toward Zero Exposure program?
- What tools has CEPN developed to support companies on their journey to reduce worker exposure to toxic chemicals?
- Where can I find resources for safer alternatives?
- Can my organization join CEPN?
- What does CEPN do?
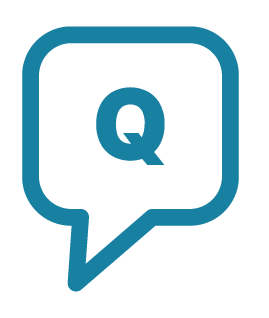
What is the Toward Zero Exposure program?
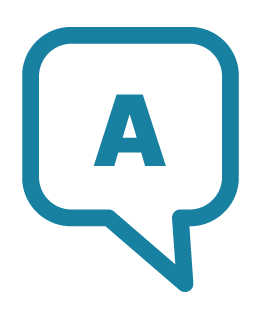
Toward Zero Exposure is a commitment program to protect workers from chemical hazards in the electronics supply chain.
It is founded with the fundamental belief that a safe, healthy work environment is a basic human right and protecting workers from exposure to toxic chemicals is the right thing to do, and requires collective action.
The program unites companies throughout the electronics industry in a journey to reduce worker exposure to hazardous chemicals. The core building blocks include commitments that companies make with their participation, principles that guide the program design and requirements and verification to document how companies implement the commitments. To find out more, visit www.towardzeroexposure.org.
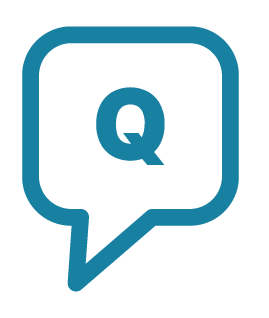
What tools has CEPN developed to support companies on their journey to reduce worker exposure to toxic chemicals?
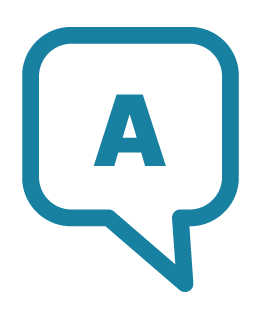
CEPN has developed the following tools which are freely available to support companies and organizations interested moving toward zero exposure of workers to hazardous chemicals and streamlining communication around safer chemical handling practices.
The Process Chemicals Data Collection (PCDC) Tool, is a standardized reporting tool that improves the task of collecting and managing process chemicals data. Network members invite all companies in the electronics industry to use the PCDC Tool.
The Qualitative Exposure Assessment (QEA) helps facilities fill in information where workplace chemical exposure data is not available. It identifies potential risk of worker exposure to harmful process chemicals within a facility.
The Alternatives Assessment Guide is a concise, high-level guide for identifying and evaluating potential substitutions for Chemicals of High Concern used in electronics manufacturing processes. The tool is intended to allow companies to thoroughly assess and implement safer alternatives to identified Chemicals of High Concern, while avoiding regrettable substitutions. A safer alternative may include a chemical substitute or a change in materials or design that eliminates the need for a chemical alternative.
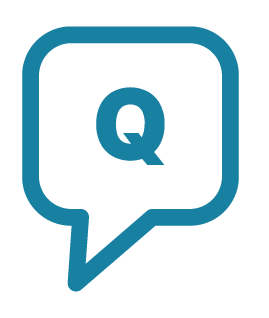
Where can I find resources for safer alternatives?
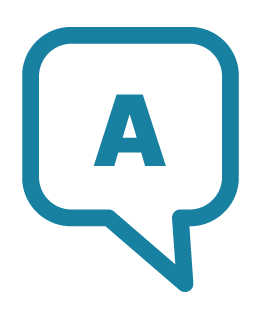
Several organizations currently certify safer manufacturing cleaning products and accepted substances as well as provide evaluation of formulations. This information is provided to assist both companies and facilities in the electronics supply chain in finding safer alternatives, and chemical suppliers in certifying chemical products. Visit our Safer Alternatives page for a list of these organizations.
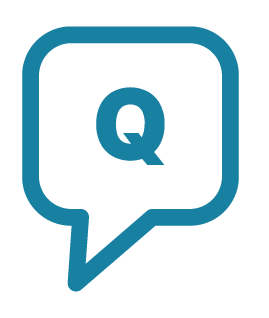
Can my organization join CEPN?
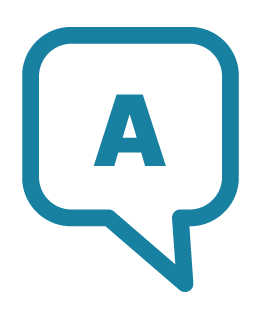
The Network welcomes diverse participants from across the supply chain who are innovators and natural collaborators, experts in their segment of the supply chain, held in high regard by their peers, and committed to the goals of CEPN. Participation in the Network is by invitation from existing members.
Participation in the Network is fee-based, with corporate and other large organization members paying fees based on annual gross revenues. These member fees support the operation of the Network and underwrite the participation of stakeholders representing workers and other NGOs.
The Network operates under well-defined antitrust guidelines and terms of confidentiality.
If you are interested in learning more about CEPN, or if you would like to be involved please contact us at info@cleanelectronicsproduction.org.
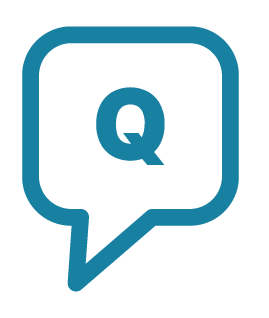
What does CEPN do?
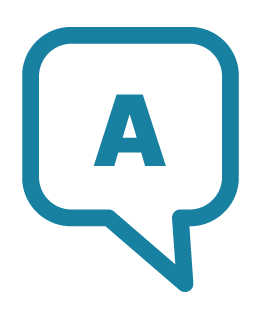
CEPN comprises more than 20 member organizations including electronics brands and suppliers, environmental NGOs, labor and worker representatives, ecolabels and representatives from academia and government agencies.
The collaborative, multi-stakeholder innovation network launched in 2016 by the Center for Sustainability Solutions at Green America to addresses complex workplace health and safety challenges in the electronics supply chain, with the goal to move toward zero exposure of workers to toxic chemicals in electronics manufacturing.